Flexible packaging systems with the highest line efficiency for single-serve packets
Perfectly dispensed single-serve packets are practical and are enjoying increasing popularity, especially for fast coffee preparation. Compostable capsules made of paper, for example, and single-serve aluminum packs are becoming increasingly popular, although plastic capsules continue to lead in some markets. No matter which material customers prefer or want to manufacture single-serve packets with tea, nutritional supplements or liquid concentrate instead of coffee capsules, Optima will supply the highly efficient and flexible standalone machines as well as high-performance turnkey systems.
Consumers are increasingly demanding sustainability, especially in the single-serve packaging sector. In addition, consumers like to have a choice between different packaging sizes. Manufacturer, have to meet these demands and at the same time face increasing cost pressures. That’s a balancing act which can easily manage with Optima Countless successful solutions for start-ups to major corporations attest to it!
Optima bring this incalculable wealth of experience to every single-serve application. Whether to fill capsules with fine powder, granulate or liquid, Optima will provide with core processes tailored to the needs from a single source – from a standalone machine to a complete line, including filling, boxing, tray packaging and palletised options.
Customised machine solutions with major advantages:
With experience and expertise, Optima will develop perfect technologies tailored to special requirements.
- Maximum format flexibility for capsules (focus on capsule type) and packaging
- Maximum system availability
- A variety of setting patterns without changeover times
- No product loss thanks to inline quality testing
- Maximum automation for faster production
- Output rates depending on the requirements profile: 100 to 2,000 capsules per minute
Single-serve packets that customers will love:
Liquid, powder or granule form – the product and requirements will determine the single-serve packaging. They are the benchmark for the entire process. For the best results and outstanding in-cup quality:
- Precise dosing
- Gentle product handling
- Reliable product protection
- Preservation of all the aromas
- Loading capsules
Pre-fabricated capsules are fed manually out of the box or by autoloader as needed. It doesn’t matter whether the capsules are aluminium, plastic or compostable. Then the empty boxes are returned and stacked.
- Fully automated process
- Gentle handling
- Easy removal of empty boxes
- Precise dosing
Optima use the appropriate dosing technology depending on whether you want to fill up with powder, granules, liquid or flavourings. Solids can be gently compressed without changing product quality. The filling process in a controlled atmosphere ensures reduced oxygen levels. One hundred percent weighing guarantees continual self-optimization of the filling weight. Fluctuations in bulk density are immediately detected and corrected.
- Precise dosing (in mg and ml)
- Reduction of product loss
- Clean capsule edges
- Tool-free format changes
- Easy exchange of parts in contact with the product
- Integrated product compression
- Punching and sealing
It can also be flexible with the material for lids: Our system processes laminates, aluminum foil, paper or filter materials from a stack or roll. Foil-saving modules ensure optimum use of material. Lids are securely sealed using thermal sealing, induction or ultrasound.
- Ceramic insulation with extremely high temperature accuracy
- 100% capsule leak test inline
- Exact lid positioning
- Optimized material use, very high level of material exploitation
- Grouping capsules
One of the most important innovations is the patented gap closer. It allows any setting pattern to be generated and the desired number to be dispensed. Every capsule has its own controllable shuttle so that the correct number of units is continuously conveyed to the correct place for the boxing machine. The best part: The system does not require a format change for a setting pattern thanks to the state-of-the-art linear motor system that reduces the footprint for the entire system as well. A format change of about 15 minutes is only required for changes to the final packaging.
- Flexible grouping
- Any setting pattern without format change
- Format flexibility
- Inline controls (flap control, weight control, vacuum control)
- Boxing
Optima’s systems erect the selected box flat blanks. The top loader carefully picks up the pre-grouped capsules and sets them into the packet – each rotated or not rotated, depending on the pattern. To separate the capsule layers, intermediary layers and or punched intermediary layers that secure the capsules can be inserted. If a box does not meet the high quality standards, the whole box is rejected; the good capsules can be returned and repackaged.
- Flexible box format: change in only 15 minutes
- Setting pattern as required without format change
- Inline laser marking of the secondary packaging
- Integrated check weigher
- Automatic insertion of different intermediate layers
- Tray packaging
The filled boxes are grouped according to the requirements and packed in trays. While doing this, we pay attention to space-saving feed technology adapted to your production space as well as efficient shapes of the trays. One-item and two-item trays marked and labeled inline are possible.
- Wrap-around tray and tray lid solution
- Wide-ranging grouping variants
- Integrated systems for product labeling and tracking
Filling and closing capsules with a small footprint
Output: 100 – 2,000 capsules per minute
The OPTIMA CFL is a flexible filling and closing system for single-serve packets made from a range of different materials. It is available in various versions, from an entry-level model to a high-performance solution with an output of 2,000 capsules per minute. But no matter which CFL is selected, the production will protect the environment and save resources thanks to optimized foil utilization, very high dosing accuracy, reduced gas consumption and extremely low energy consumption.
- OPTIMA CFL1: The compact one
With the compact CFL1, can produce up to 360 capsules per minute
- OPTIMA CFL10: For a little more
The CFL 10 processes up to 780 capsules per minute.
- OPTIMA CFL40: The high-speed solution
The CFL40 processes up TO 2,000 capsules per minute
Major advantages
- Maximum machine efficiency
- Very high material exploitation
- Flexibility: aluminium, plastic and compostable capsules
- Safe gassing with minimized gas consumption
- Expandable modular design for future adjustments
- Vertical start-up for direct production with highest efficiency
A boxing machine for a wide range of setting patterns without format changes
Output: up to 250 boxes/minute
The OPTIMA CBF high-performance boxing machine offers maximum setting pattern flexibility and can be switched to other box sizes in no time at all. This is made possible by its state-of-the-art linear motor system that reduces the footprint of the entire production line.
Each capsule has its own controllable shuttle that facilitates individual groupings. This always allows exactly the desired number of capsules to be conveyed to the boxing machine.
The OPTIMA CBF offers
- A minimized footprint
- Capsule groupings as required without a format change
- Gentle handling of the capsules due to integrated robotics
- Integrated check weigher
- Integrated space-saving control cabinets
Low energy consumption due to vacuum switch-off
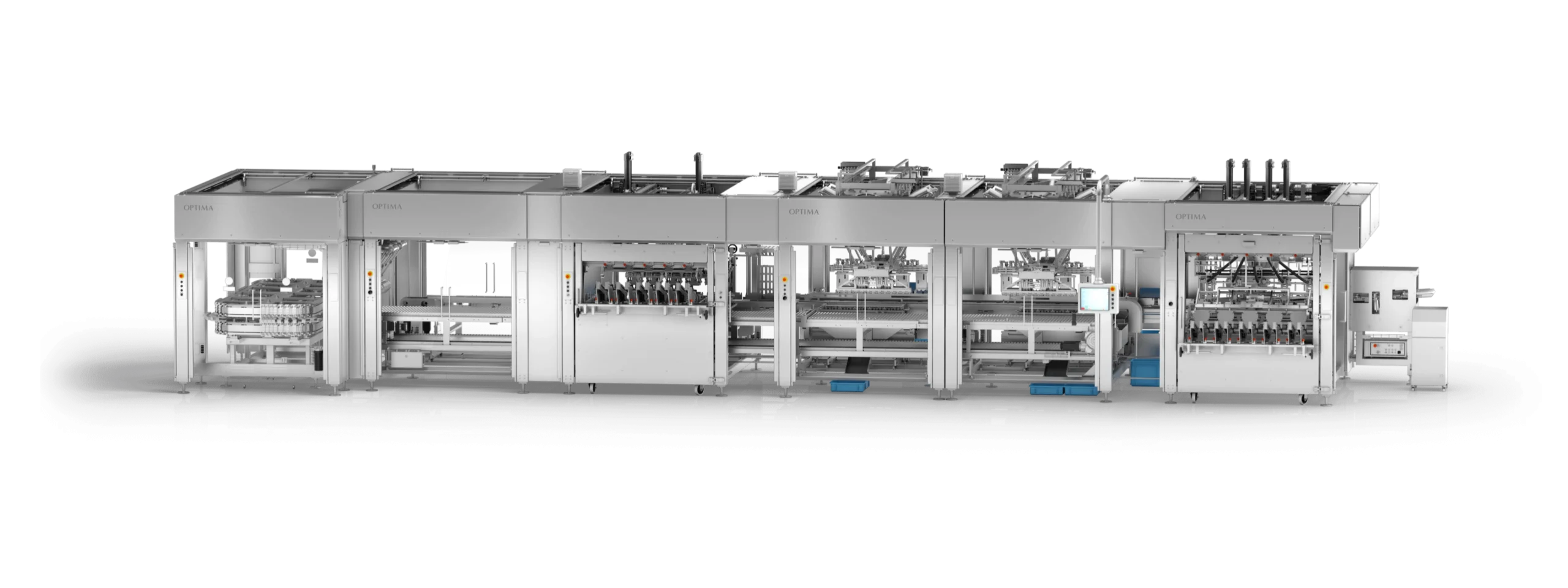
A case packer for maximum efficiency inline
Output: up to 15 trays/minute
The OPTIMA TMF casepacker pre-groups the boxes from the OPTIMA CBF and then packages them in one-item or two-item trays. The trays are labeled and marked inline. Developed for integration into production lines, the OPTIMA TMF works perfectly with other machines in the line.
The OPTIMA TMF offers
- One-item and/or two-item trays
- Very large format range
- Integrated labeling module
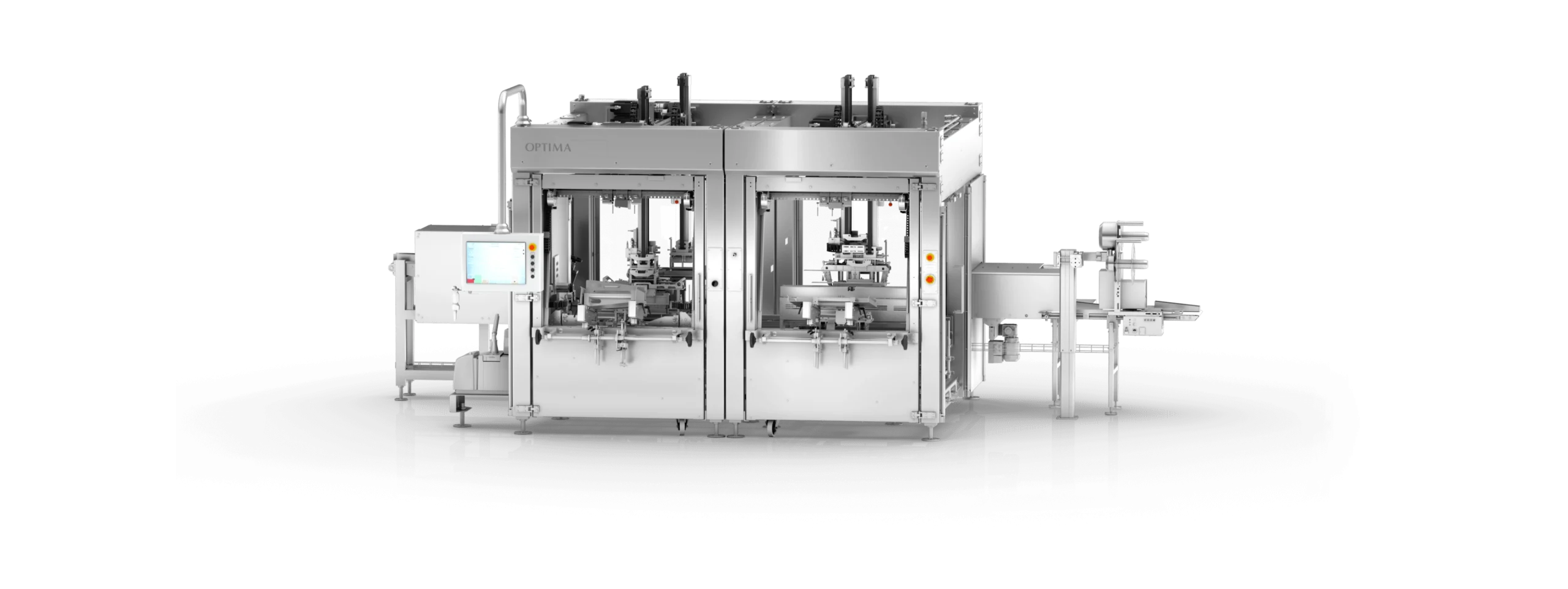
The efficient compact solution for a fast entry level
Output: up to 220 capsules/minute
Whether new on the market or contract filler, the OPTIMA CFR will give a decisive edge: Thanks to its modular, configurable design, it can have production up and running in just a few months so that can quickly and safely get capsules to the point of sale. It also takes up little space, because the control cabinet is built-in. The “balcony design” provides optimum accessibility and makes cleaning and maintenance easier. The required functional units can be arranged.
The OPTIMA CFR offers
- Fast delivery time
- Very good accessibility
- Easy cleaning, maintenance and operation
- Plastic, aluminium and compostable capsules
- Modular and configurable
- Minimal space required thanks to the built-in control cabinet
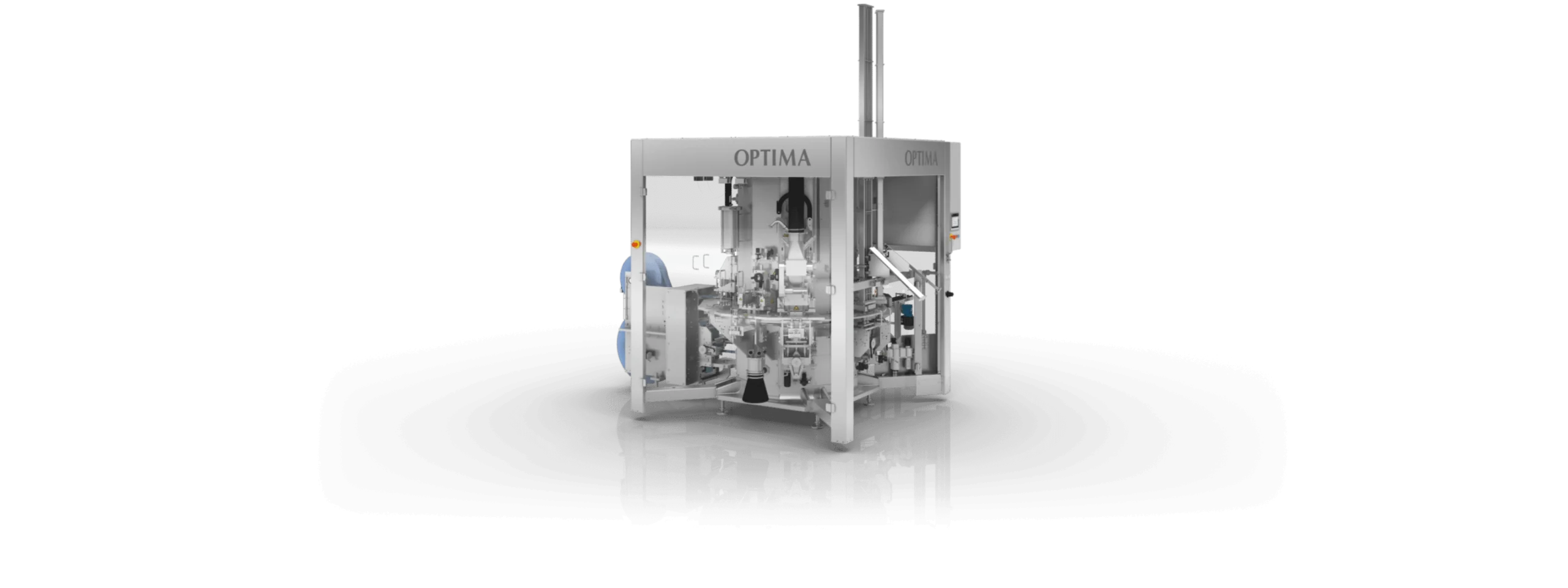